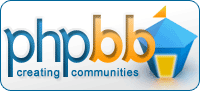 |
Cigar Funhouse Cigars, and all things related - brought to you by Richmond Avenue Cigar
|
View previous topic :: View next topic |
Author |
Message |
seolinks786
Joined: 06 Dec 2022 Posts: 431
|
Posted: Tue Oct 22, 2024 3:41 pm Post subject: Comparative Analysis of Conveyor Systems for Heavy-Duty Appl |
|
|
Conveyor systems are critical for the efficient movement of materials in heavy-duty applications, particularly in industries like metalworking, mining, and manufacturing. With various Shredder Wringer Chip Processing Equipment types of conveyors available, each designed for specific tasks, it’s essential to understand the strengths and weaknesses of each system. This article provides a comparative analysis of different conveyor systems used in heavy-duty applications.
Types of Conveyor Systems
1. Belt Conveyors
Belt conveyors are one of the most widely used types of conveyor systems in heavy-duty applications. They consist of a continuous loop of material, usually made of rubber or fabric, supported by pulleys. Belt conveyors are ideal for transporting bulk materials over long distances and can handle a variety of materials, including metal chips, powders, and aggregates.
Pros:
Versatile and suitable for various materials
Efficient over long distances
Simple design and operation
Cons:
Limited in incline and decline applications
Prone to slippage if overloaded
2. Screw Conveyors
Screw conveyors utilize a rotating helical screw blade to move materials along a tube. They are particularly effective for handling bulk materials that are granular or powdery, such as metal turnings or shavings.
Pros:
Compact design, suitable for tight spaces
Effective for inclined transportation
Less prone to material spillage
Cons:
Limited capacity compared to other systems
Wear and tear on the screw can lead to maintenance issues
3. Chain Conveyors
Chain conveyors employ a series of chains to move materials along a track. They are well-suited for heavy loads, making them ideal for transporting metal parts and components.
Pros:
High load capacity
Durable and resistant to heavy impact
Suitable for harsh environments
Cons:
More complex installation and maintenance
Limited flexibility in design
4. Magnetic Conveyors
Magnetic conveyors use magnets to move ferrous materials along a belt or surface. They are particularly useful for handling metal chips and scrap, as they securely hold materials in place during transport.
Pros:
Effective for transporting small and irregularly shaped metal parts
Reduces the risk of spillage
Ideal for processing metal turnings
Cons:
Limited to ferrous materials
Higher initial investment compared to other systems
5. Pneumatic Conveyors
Pneumatic conveyors use air pressure to transport materials through a pipeline. They are suitable for handling dry bulk materials and can be designed for both vacuum and pressure systems.
Pros:
Minimal physical footprint
Versatile for various materials
Reduces dust and spillage
Cons:
Higher energy consumption
Potential for material degradation if not properly designed
Factors to Consider When Choosing a Conveyor System
Load Capacity
The chosen conveyor system must meet the load requirements of the specific application. Systems like chain and belt conveyors can handle heavier loads, while screw and magnetic conveyors may be more suited for lighter materials.
Material Type
Different conveyors are designed for specific types of materials. For instance, magnetic conveyors excel in moving ferrous materials, while pneumatic systems can handle a wider variety of dry bulk materials.
Space Constraints
The available space for installation can significantly influence the choice of conveyor system. Compact systems like screw conveyors may be preferable in tight spaces, while belt conveyors are more suited for longer distances.
Maintenance Requirements
Understanding the maintenance needs of each conveyor type is crucial for long-term efficiency. Some systems may require more frequent maintenance and part replacement, impacting overall operational costs.
Cost and Budget
Initial investment and ongoing operational costs should be carefully considered when selecting a conveyor system. While some systems may have a higher upfront cost, their efficiency and lower maintenance requirements could lead to long-term savings.
Conclusion
Choosing the right conveyor system for heavy-duty applications involves careful consideration of various factors, including load capacity, material type, space constraints, maintenance needs, and budget. By understanding the strengths and weaknesses of each type of conveyor, manufacturers can make informed decisions that enhance efficiency and productivity in their operations. Investing in the appropriate conveyor system is essential for streamlining material handling processes and ensuring smooth production flows. |
|
Back to top |
|
 |
|
|
You cannot post new topics in this forum You cannot reply to topics in this forum You cannot edit your posts in this forum You cannot delete your posts in this forum You cannot vote in polls in this forum
|
|